Using Artificial Intelligence to Drive Predictive Maintenance: How Intelligent Algorithms Are Protecting Industry from Downtime
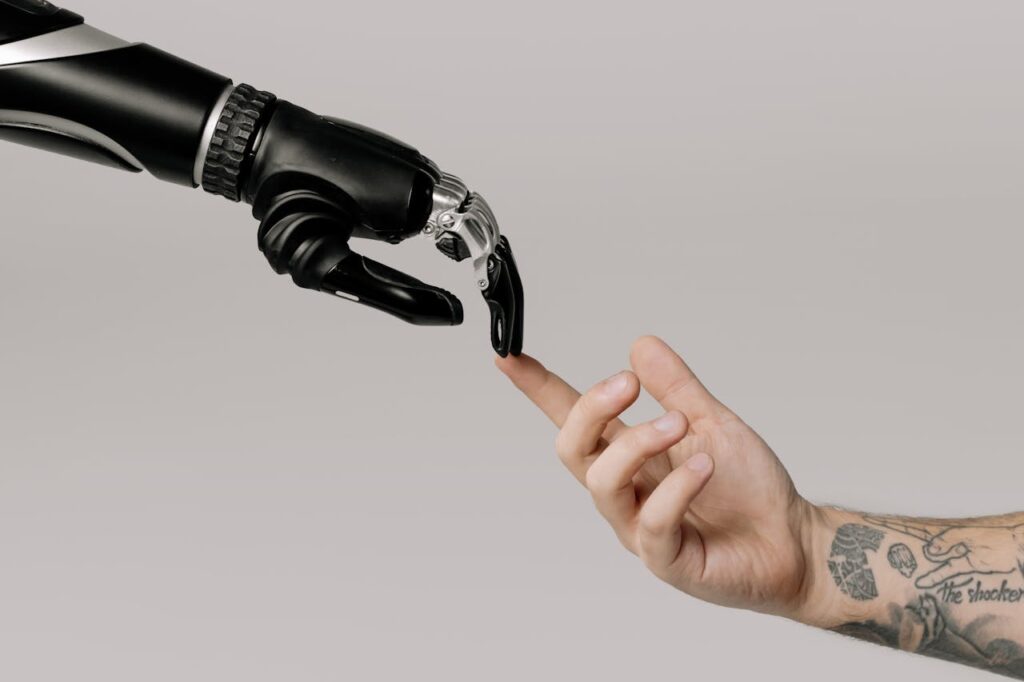
Using Artificial Intelligence to Drive Predictive Maintenance: How Intelligent Algorithms Are Protecting Industry from Downtime
It is difficult to find a single issue in the world of contemporary industry that is more disruptive and expensive than an unexpected breakdown of equipment. The effects of a single malfunction on a manufacturing line may be felt across a whole business, to the point where output is halted, deliveries are delayed, and repair expenses are increased. Scheduled maintenance, which includes the replacement of components and the performance of inspections at certain intervals, has been depended upon by industries for decades. AI-driven predictive maintenance, on the other hand, is a new strategy that is developing as technology continues to advance. This approach is smarter, more efficient, and often more cheaper. Companies are starting to anticipate issues before they occur by merging machine learning algorithms, sensors, and real-time data. This helps to avoid downtime and transforms the way in which industries maintain their machinery operating.
From Predictive Precision to Scheduled Maintenance and Maintenance
Reactive maintenance, in which repairs are performed after the equipment has failed, and preventive maintenance, in which service is performed at predetermined intervals regardless of the actual state of the unit, are the two primary categories that make up traditional maintenance plans. Although preventative maintenance is preferable than waiting for failure, it often results in the replacement of parts that are not essential or the failure to notice problems that arise in the intervals between inspections.
Predictive maintenance, which is driven by artificial intelligence, completely alters this method. Intelligent algorithms continually evaluate data from equipment sensors, measuring factors like as temperature, vibration, pressure, and sound. This is in contrast to the traditional method of depending on predetermined timetables. Whenever these algorithms identify minute alterations, which often precede failure, they have the ability to notify maintenance staff so that they may investigate or take action before an expensive breakdown happens. With this technique, which is driven by data, maintenance activities are aligned with the real health of the equipment, which saves both time and money.
What Artificial Intelligence Can Do to Make Maintenance Smarter
The capacity of artificial intelligence to see patterns that human eyes or conventional analytics would overlook is one of the reasons why it is particularly useful in predictive maintenance. The massive amounts of operational data that are generated by modern industrial machinery occur every single second. With the use of this historical and real-time data, artificial intelligence algorithms are able to learn and recognize early warning indications that often occur before to certain failures. Over the course of time, these models adjust to their environment, becoming increasingly more precise as they are provided with more data.
An example of this would be an artificial intelligence system coming to the realization that a minor but regular rise in motor vibration often occurs a few weeks before bearing breakdown. If maintenance workers are able to identify this pattern early on, they will be able to replace the bearing during regularly scheduled downtime rather of having to respond to an unexpected shutdown. In addition to minimizing downtime, this strategy has the potential to increase the lifetime of the equipment and enhance safety by eliminating unexpected occurrences of failures.
Predictive maintenance has been shown to be beneficial to several industries.
The manufacturing industry is one of the most prominent industries taking use of predictive maintenance, particularly in production lines where the costs associated with downtime may be substantial. Maintenance that is powered by artificial intelligence enables firms to maintain their machinery operating smoothly, schedule servicing only when it is required, and avoid suddenly stopping production.
Additionally, there has been a considerable increase in the generation of energy, which includes wind farms and power plants. Sensors and artificial intelligence, for example, are able to identify early warning signals of turbine wear or imbalance, which enables repairs to be arranged during times when there is a lower demand for electricity. To a similar extent, predictive maintenance is used in the transportation and logistics industry to ensure that fleets of trucks, trains, and airplanes continue to function effectively, hence enhancing dependability and minimizing interruptions to service.
For the purpose of continually monitoring assets and reducing the need for human inspections, even sectors such as mining, oil and gas, and utilities are becoming more reliant on AI-driven solutions. This is because these industries often run equipment in distant or dangerous regions.
The Importance of Internet of Things and Big Data
Without advancements in data storage and processing, as well as the expansion of the Internet of Things (IoT), it would be impossible to do predictive maintenance that is driven by artificial intelligence. Sensors that are built into machines are able to collect data in real time, including vibration, temperature, pressure, and humidity from the machine. All of these data points are then sent to central systems, where they are processed and analyzed by artificial intelligence models.
Large-scale data infrastructure gives businesses the ability to store and handle massive amounts of information over the course of several years. With the aid of this long-term data, artificial intelligence is able to better learn what “normal” looks like for each piece of equipment, which improves its ability to spot abnormalities.
The Obstacles That Stand in the Way of Adoption
Even while it has a lot of potential, putting AI-driven predictive maintenance into practice is not without its challenges. Especially in older factories, where legacy machines do not have built-in sensors, it might be difficult to collect data of a high quality and consistency from a wide variety of equipment. Time, competence, and a substantial quantity of historical data are all necessary components for the development and training of efficient artificial intelligence models.
Moreover, a transformation in culture is required in order to successfully incorporate AI insights into day-to-day operations. It is imperative that maintenance teams acquire the ability to trust suggestions given by machines and modify their schedules to accommodate a workflow that is driven by data rather of the more conventional calendar-based inspections.
In the future, there will be fewer instances of failure.
With the maturation of artificial intelligence technologies, it is anticipated that predictive maintenance will become increasingly more accurate and widely utilized. The capabilities of future systems may extend beyond the prediction of failures to include the recommendation of ideal operating conditions that decrease wear, the autonomous scheduling of repairs, and even the ordering of new components on their own.
It is not merely the cost reductions that are the source of this evolution’s excitement; but those savings might be significant nevertheless. It is about changing maintenance from a reactive or routine duty into a strategic advantage, which includes equipment that virtually never stop suddenly, manufacturing lines that function more effectively, and industrial personnel who are freed from repeated inspections so that they can concentrate on higher-value duties.
An Industry That Is Both Smarter and More Reliable
Predictive maintenance that is powered by artificial intelligence is at the intersection of machine learning, the internet of things, and industrial knowledge. Through the transformation of raw data into meaningful insights, it enables businesses to anticipate issues before they occur, so preventing downtime and ensuring that key equipment remains in optimum condition. The advantages, which include reduced expenses for maintenance and a longer life for the equipment, as well as improvements in safety and productivity, are already creating a compelling argument for change, despite the fact that hurdles still exist. Predictive maintenance is expected to become less of a notion from the far future and more of a reality that is experienced on a daily basis as companies continue to embrace artificial intelligence. This will ensure that the wheels of industry continue to revolve without interruption.